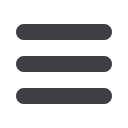
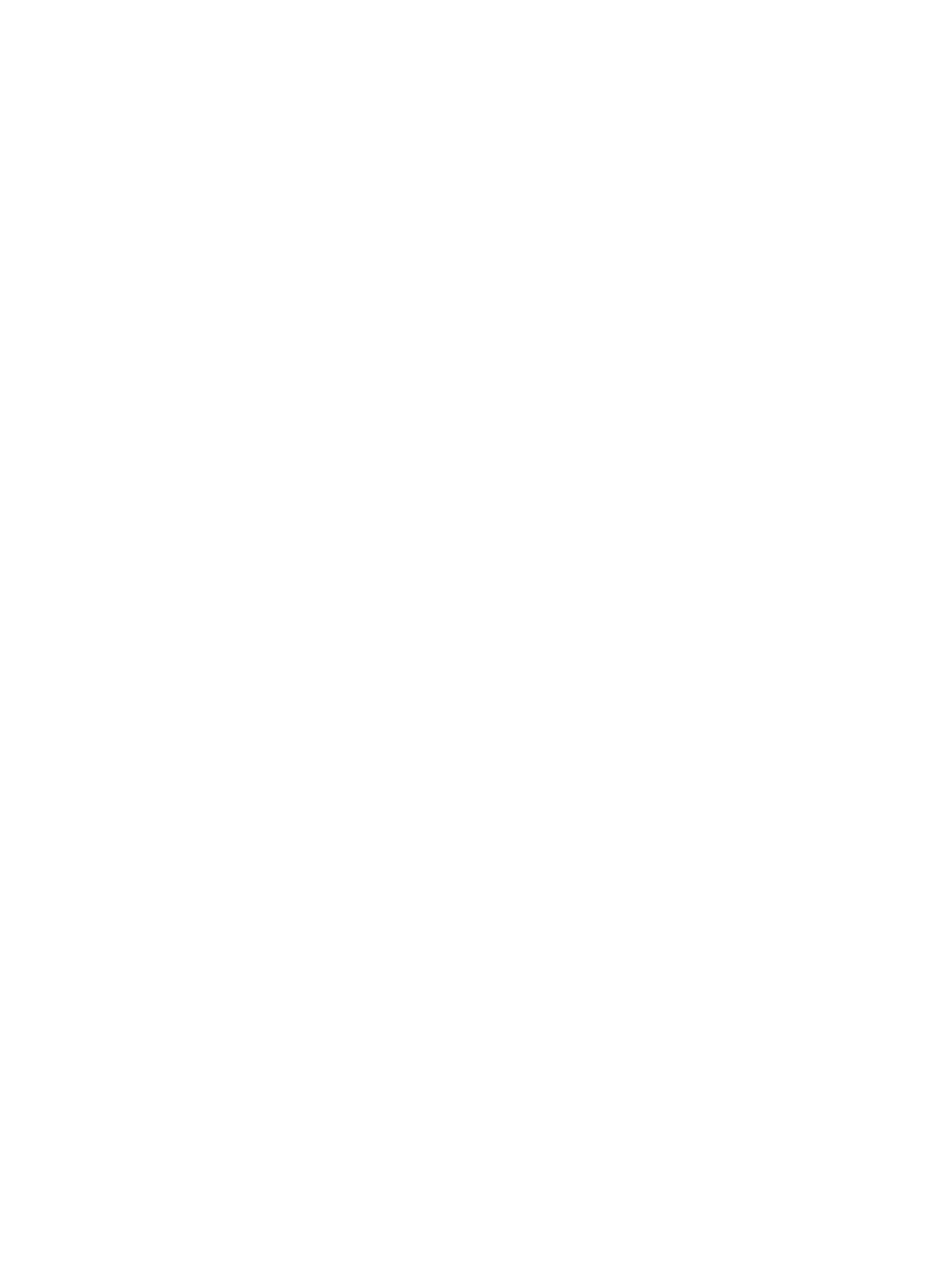
臺大管理論叢
第
27
卷第
3
期
5
(Fujimoto, 1999). The use of sophisticated, single-purpose machines and semi-skilled or
unskilled workers greatly increased productivity (Womack et al., 1990).
MPS was the accepted standard as the best practice in the automobile industry, until
Taiichi Ohno and his
Toyota Production System (TPS)
(also called
Lean Manufacturing
)
joined the competition in 1950s. Far ahead of his peers using MPS manufacturing, Ohno
identified and examined the flaws of MPS, experimented with alternative processes and
devised a new system (Fujimoto, 1999). Mass producers had added many buffers to the MPS
production system to ensure smooth production since the machinery was expensive and
costly to fix production disruptions; in contrast, the revolutionary TPS employed just-in-time
production and flexible machines to minimize the buffers, eliminating wastes of materials,
machine time and worker hours (Schonberger, 2007). In essence, TPS is a synthesis of CP
and MPS, but without the high cost as the CP system or the rigidity of the MPS system
(Womack et al., 1990). Ultimately, TPS
ʼ
s superior productivity, quality, and flexibility
successfully challenged the MPS practice in the industry.
Surprisingly, we observe in practice that the manufacturing leaders today deliberately
explicate their processes to attract challengers’ improvement efforts. The resulting
constraints on challengers’ process innovation capability development ultimately decrease
the threat to the leading firms. For instance, the apprenticeship in the CP age, which enabled
the greatest access to the leading process, did not trigger process innovation for hundreds of
years. Furthermore, consider Toyota’s openness to opening its process to its rivals via factory
tours. Many rival firms have visited Toyota’s factories and consequently developed “Toyota-
like” operational processes with small improvements. Despite their efforts to replicate
Toyota’s success, its rivals have not been able to match Toyota’s systematic improvement
process, which continuously improves quality and cost competitiveness (Schonberger, 2007).
To date, TPS remains the industry leader in process management and has been for over fifty
years. In short, the pressure from competition prompts the leader to defend itself, for
example, by “locking” rivals into small-scale process improvement.
3. Theoretical Background
Anecdotal evidence suggests that the firm generates a superior process that evolves
during its interactions in competing with competitors
ʼ
processes over time. The literature
identifies two possible tensions in process competition. One is between competing processes
(a firm’s current process versus its rival’s process) from the external view of competition in
business strategy (Porter, 1980). The other tension derives from the internal view of